The main implementation standards
GB/T 3836.1-2021 Explosive atmospheres – Part 1: Equipment – General requirements
GB/T 3836.2-2021 Explosive atmospheres – Part 2: Equipment protected by flameproof enclosure "d".
GB/T 3836.4-2021 Explosive atmospheres – Part 4: Equipment protected by intrinsically safe type "i".
GB 40881-2021 Code for the design of safety guarantee system for low-concentration gas pipeline transportation in coal mines
AQ 1073-2009 General Technical Conditions for Automatic Explosion Arresting Device for Gas Pipeline Transportation
Schematic diagram of the installation of safety facilities for gas power generation pipelines
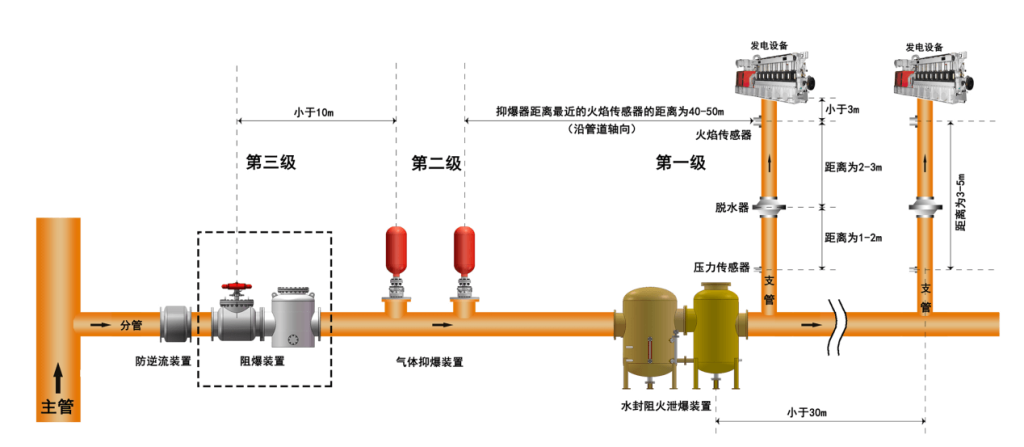
System functions and features
Flame signal detection: multi-band spectral detection, using imported photosensitive tubes and military manufacturing quality, to ensure that the flame sensor accurately detects flame signals. | Shock wave signal detection: high-frequency dynamic pressure detector, high frequency response, fast speed, accurate detection of shock wave signal generated by explosion. |
Visualized centralized control: Based on the visual comprehensive display, through accurate detection of fire data, equipment status display, equipment failure and other diagnostic analysis, intelligent early warning, troubleshooting and other automatic control are realized. | Accurate analysis and reliable execution: The sensor transmits the detected fire signal to the controller, and the controller reliably drives the action of the explosion suppressor through precise algorithms and accurate logic analysis and judgment. |
Multi-channel linkage control: The system can be connected to up to 10 flame sensors, 10 shock wave sensors, 5 pressure sensors, and can drive 5 explosion arrest valves at the same time to achieve multi-pipeline fire extinguishing and explosion arrest control. | Intelligent system operation and maintenance monitoring: Visualized monitoring technology is used to intuitively and comprehensively monitor the fire situation of gas transmission pipelines, comprehensively analyze and evaluate subsystems at all levels of explosion suppression, explosion arrest and explosion venting, and dynamically analyze the safety situation. |
- 1 Fast response time of sensor control: T<1ms
- 2. Large-capacity lithium battery for backup: 10000mAh
- 3 Multi-band spectral detection technology: 4-band spectroscopy
- 4. Shock wave detection technology: high-frequency dynamic pressure detection
- 5. Multi-channel sensor monitoring: up to 25 sensors are connected
- 6 Multi-way drive control: up to 5-way drive explosion-arresting valve
- 7. Material control: Stainless steel material is preferred
- 8 Safe and fast: high-pressure nitrogen actuates the valve to close
- Monitoring during bottle compaction: to ensure that the condition of the explosion arrest valve is valid
- 9. Multi-interface display: LCD and LED interface display
- 11. Multiple data uploads: RS485/CAN communication
- 12. System intelligent early warning: comprehensive analysis and evaluation dynamic display